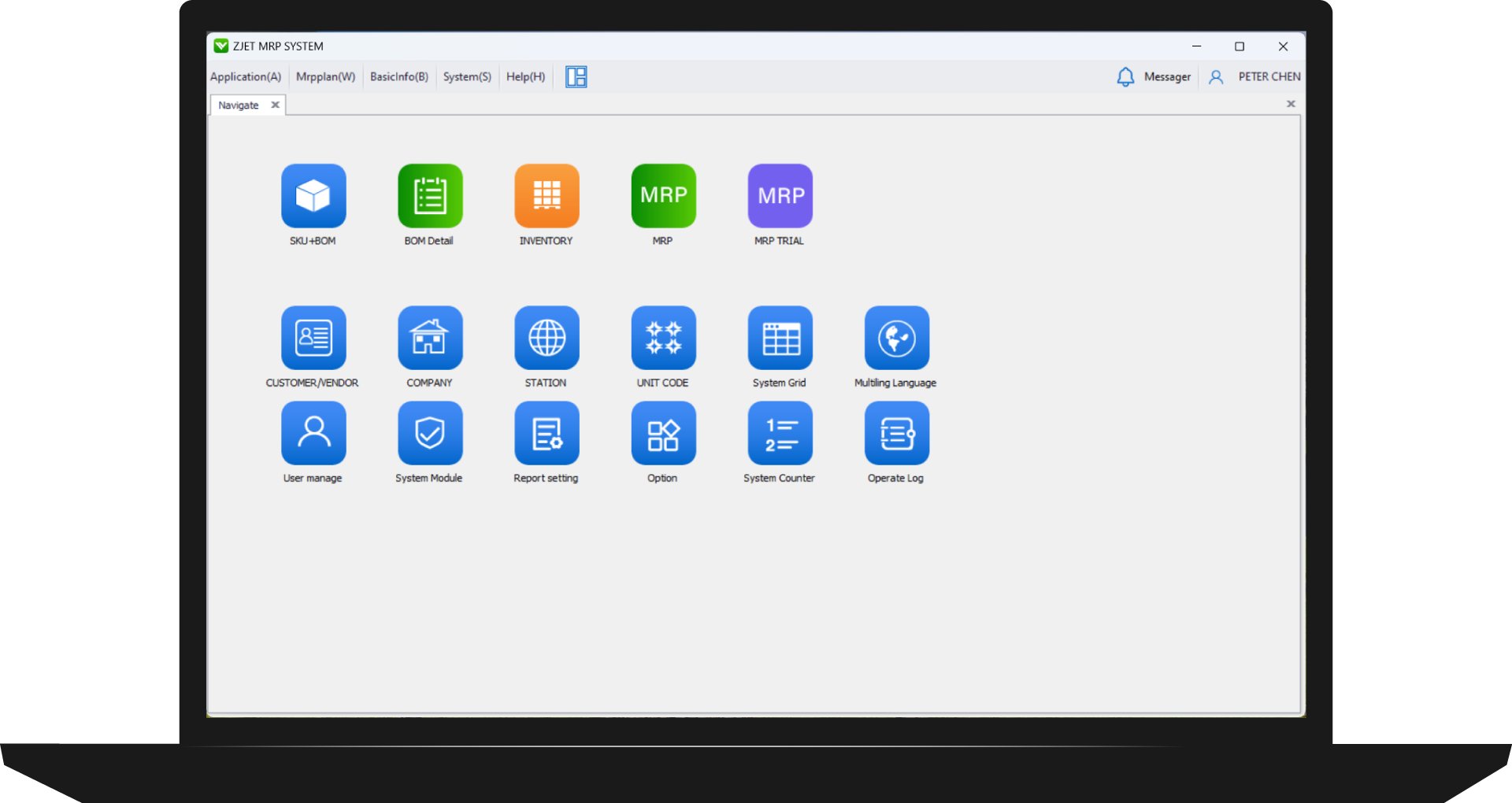
Specially designed for small and medium-sized trading companies, processing plants, professional warehousing companies to design material requirements and order procurement calculation system.
Integrate basic material information, production or purchase leadtime, finished goods bill of materials (BOM), combine available inventory with defined material purchase orders and demand planning, and quickly generate missing material details as well as planned purchase order quantities and purchase dates.
With the part number + version as the unique index value, the basic information is established for each finished product and material, including different versions, and the material information includes production, transportation, testing and other production time, which is used to calculate the estimated order time.
Establish bill of material for each finished product, which can record the alternative part number of each material at the same time, so as to realize the multi-version management of finished products and materials.
The available inventory can be obtained by EXCEL import or EDI transmission in combination with other systems, and can be used as the basic data for MRP calculation, and can be recorded by warehouse or branch for multi-warehouse or multi-company inventory.
Recording orders that have been confirmed by the supplier but not actually delivered is also one of the basic data for MRP to calculate the scheduled purchase order.
Accurate to the week, record the customer's finished product demand, can be managed by week, can also be managed by day, need to have the finished product version number, is one of the key data to calculate the material requirement plan, as well as to produce the details of the shortage.
Accurate to the day, this is a collection used to calculate the underpayment details according to the specific production date, and the underweight details can be calculated for each day.
Through inventory, confirmed undelivered orders, combined with demand planning, calculate the date of production arrears, and calculate the latest date of the expected order based on the number of days before the production or purchase of the material, and generate a list of estimated purchase orders.
The function is the same as the material requirement calculation, except that the inventory and production plan can be adjusted and imported as the basis for calculation, and then the demand trial calculation can be used for the calculation of the ECN predetermined time of the product, the calculation of substitute materials, etc.
By marking the ECN change of old materials in the BOM, and establishing different versions of the finished product BOM according to the switching plan, after the material requirements calculate the latest date of the actual inventory available, export the ECN date report, and import the ECN date into the formal demand calculation according to the date as the switching version date, so as to complete the ECN switching.
It can manage orders for trading companies, combine inventory, consolidate orders, and calculate the quantity and order date for predetermined purchases.
It can provide a complete set of data management for processing enterprises, from material information, bill of materials, to inventory management, to production planning, to realize the calculation of material requirements.
It provides the function of calculating the undersupply for warehousing enterprises engaged in packaging business, which is convenient for reminding customers to replenish materials in time and ensure the normal operation of the packaging line.
Simple, easy to use, efficient
18 months demand, 70 materials, 10 kinds of finished products, a material calculation takes 3 seconds to complete.
Excellent algorithm design, easy to configure, change the algorithm at any time, and can be calculated after the client imports, simple and easy to use.
It can manage multi-company, multi-site material requirement calculations, and generate a variety of reports based on MRP calculation results.